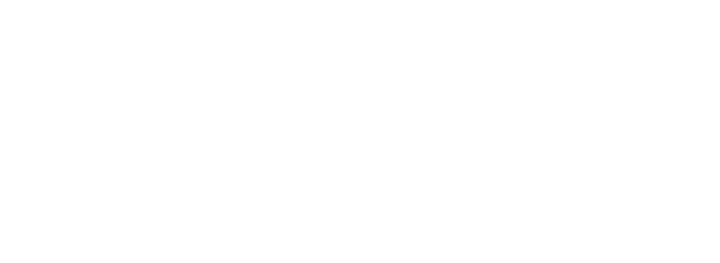
-
1 原材料复检
原材料入厂后,公司按相关标准对原材料复检,确保产品源头质量稳定。
-
2 原材料锯切下料
锯切区采用奥地利林辛格高速圆盘锯,具备自动体积测量、称重等功能,质量控制精准,重量偏差仅有±1KG,具有80件/小时的锯切下料能力。
-
3 环形炉加热
直径24M环形加热炉满载布料达360件,利用天然气加热,通过脉冲比例控温实现温度均匀性±10℃,出炉温度1250℃,具备每小时出料80件的加热能力。
-
4 车轮预成型
车轮预成型在50MN框架式油压机上完成,压至工艺要求高度后实现金属的第一次a分配。
-
5 车轮成形
车轮成形在100MN框架式油压机上完成,实现轮毂、辐板及轮辋的金属第二次分配。
-
6 车轮轧制
成形后轮坯放入DRAW1250轧机进行轧制,使辐板、轮辋、轮缘等部位达到有效成形结果,轧制精度可实现±1mm。
-
7 车轮压弯冲孔
轧制后轮坯放入50MN框架式油压机,完成轮坯辐板及轮辋的最终成形,通过冲孔实现芯料与车轮本体分离。
-
8 热态标识打印
通过信息系统将车轮炉号、钢坯号等身份信息利用热态打标机打刻于车轮表面,实现身份信息转移。
-
9 热锻件几何尺寸测量
锻轧线配备了热态三维激光测量设备,在1150℃高温下可以直观、清晰的判断产品成型质量,及时反馈,实现参数调整。
-
10 车轮淬火加热
通过隧道加热炉,实现车轮退火、淬火加热、回火处理,利用脉冲比例控温实现温度均匀性±5℃,整个热处理过程由信息化系统自动跟踪运行。
-
11 车轮淬火处理
淬火系统可自动控制水温、水压、水量,实现淬火参数在线监控,有效保障产品硬度均匀性、一致性和稳定性。
-
12 车轮机加工
车轮加工采用德国汉根赛特加工、钻铣中心,每台加工中心自带量仪可实现单件车轮全自动单独加工,加工精度高可控制在3μm以内。
-
13 车轮静不平衡检测
通过离心法精确测量车轮残余静不平衡值,可直接反应出加工水平,确保车轮高速运行稳定性。
-
14 车轮表面硬度检测
使用3000kg的压力对车轮轮辋表面进行布氏硬度测试,保证车轮耐磨性能。
-
15 车轮表面质量目视检查
采用双工位目检台,可多角度检查车轮表面质量,并对关键和特殊尺寸进行测量。
-
16 车轮全尺寸自动测量
利用激光三维测量法快速实现车轮几何尺寸和公差在线检测,避免人为因素干扰,测量精度可达0.01mm。
-
17 车轮内部缺陷超声波检测
采用水浸相控阵超声波检测技术,可高精度、省盲区、快速检测车轮内部缺陷,排除车辆运行隐患。
-
18 车轮表面缺陷磁粉检测
荧光湿法磁粉检测车轮表面及近表面缺陷,可直观的发现肉眼在常规状态下不易发现的缺陷,确保车轮品质。
-
19 成品包装发运
为保证产品的可追溯性,在产品轮毂表面打刻能够识别其身份的流水号,车轮交付客户后可根据流水号查询到产品全部生产制造信息。
-
20 成品包装发运
采用自动化智能分包系统,可依据预设条件完成车轮自动分类、落垛。整条检测线通过德国制造机械手贯穿始终,能够实现快速、精准的物料传递,同时实时采集车轮检测信息,检测过程一目了然。